In June, while based in Copenhagen testing soil ratios, we searched naively for the magic ratio of clay, sand and aggregate. Ratios ranged from source to source. When the eight big bags of clay soil ordered from Solum arrived, we queried why they had delivered sand: the soil from Roskilde, on the north of Zealand, was yellow, grainy and sandy to touch. This was our first introduction to the richness and variety of soil types across the world. Many failed tests later we understood that the clay content of this Danish soil was low. We learnt the ratio would come to depend on the makeup of the local found ground.
Every rammed earth building is as unique as the geology beneath it. Turning that geology into architecture requires a recipe: the ingredients and the method that allow one to build consistently with a non-standardized material to modern standards. The ingredients—silt, sand and gravel as the compressive constituents and clay as the binding matter—are universally available. The challenge is finding them in the right ratios. This method describes how the ingredients from a building site can be prepared into ready-to-ram loose earthen material. Developing a rammed earth recipe is a process that adapts with each new project. There is no one-size-fits-all approach. The ever-changing subsoil composition, construction type, local infrastructure, labor force, project size and timeline all influence the design of the recipe. In bygone times, the range of earth that was built with was broader. Legal and reputational risks now dictate a more precise and standard specification of the recipe, and this can mean more adaptation to the local excavation material. Developed over 35 years, the steps given here are a general outline of the workflow Lehm Ton Erde follows when creating a new recipe. Gaining understanding through experimentation—tacit learning by feeling the material—is an irreplaceable part of grasping the rammed earth recipe process. The best approach is to just play in the mud.
Step 1: collecting a sample
It is essential that the material for building comes from beneath the topsoil. A rammed earth mix must contain almost no organic material, such as humus. This usually means digging down about half a meter to reach the subsoil layer. Often, some sort of earthworks have already taken place on-site and a heaped mound of dirt is perfect for sampling. The collected material must be representative, so a number of samples from across the plot is most useful. To ensure the final mix is homogeneous, the excavated material available should be enough for the entire project. Excavation works dig through several sedimentary layers—earth from different geological periods—but material should be collected and grouped from a single depth. This helps ensure minerals are of the same type and color.
Step 2: sample assessment
Often, a geotechnical report is already available for review. This is a good starting place for understanding the soil composition. This alone is not enough, though, and collecting a physical sample is unavoidable.
Get a good sniff of the loam sample: organic material from topsoil usually produces an odour, so its absence is a good sign. If the loam contains rocks and gravel, the makeup can be judged by sieving it, trying to separate the larger constituents from the fines: particles below a few millimetres in diameter. The fines—clay, silt and sand—are inseparable in a practical sense, so they are categorised as “binding and compressive” material. The sieved-out rock is purely “compressive.” Taking a handful of earth-moist loam and compressing it in the palm of the hand offers a quick indication of the binding capacity and therefore clay content of the material. The stickier, the higher the clay content. By separating the constituents and getting a feel for the clay content in a sample, it is possible to predict which ingredients need to be increased or decreased.
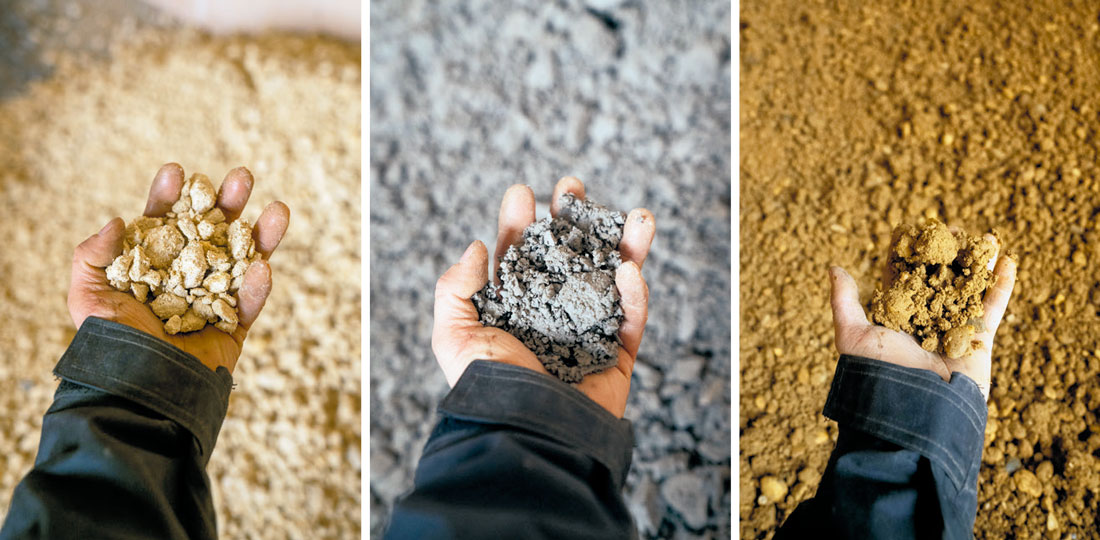
Photo by Lorenz Kastner
Step 3: systematic documentation
As the material is assessed and the recipe begins to develop, document findings systematically. For each constituent, the type of material, grain size, color, bulk density, source and distance to site should be recorded. This final piece of information helps determine the logistical impact of additional off-site material. When trialling mixtures, the parts added can be recorded like a cocktail recipe. For example, two parts site loam, one part sharp sand, two parts gravel, stirred not tumbled.
Apart from controlling quality, batches of mixes with slightly varying constituents or from different excavation sites can result in obvious tonal changes in finished walls. Clay gives rammed earth its color, for the most part. However, in cases where the walls are exposed to weathering, after some years of erosion, the fine clay washes out of the surface exposing more aggregate. This results in the weather-facing walls changing tone and texture to the predominant appearance of the aggregate content. This does not happen uniformly on a building and should be considered during recipe development.
Step 4: recipe development
An even distribution of small to large grain sizes of aggregate is important for good compressive strength. A grain size analysis of a sample can be conducted by a lab which graphs the different particle sizes and their distribution on a curve and can inform the development of a recipe. However, a range of curves work, so it is faster and more pragmatic to make several mixes and develop the best recipe through trial and error. If mixing is to be done by hand, the excavated loam should be dried in order to pulverize it and accurately introduce water content into a mix. Aggregate must be angular in geometry rather than rounded and mixing two different clayey materials can achieve better results. As batches of earth are mixed, with slightly differing ratios of ingredients, many criteria must be satisfied at once. Adjusting one component of the recipe to meet one criterion can have effects on other criteria. Experience is the only way to learn this. Some criteria can’t be assessed until after samples have been rammed and dried. Criteria to consider when creating a mixture include:
– Compressive strength
– Sustainability of mix
– Erosion resistance
– Workability of material
– Availability of material components
– Cost of material components
– Ease of replicability
– Resistance to cracking
– Expression of horizontal texture
– Resistance to cracking
– Tonality
– Mineral deposition on surface
Step 5: mixing procedure
The mixing procedure has as much impact on the strength and quality of the rammed earth as does its makeup. The aim is to coat each larger grain of gravel in a surface of smaller grains bound by the clay. Start with a dry mix, which includes all the constituents turned together in a dry state. It is sometimes helpful to wet the gravel before combining with the rest of the ingredients to ensure a good coating of loam covers the aggregate. When possible, this dry mix can be made in a large enough quantity to supply the entire project and stored under cover. A day before ramming is scheduled, moisten the dry mix with a hose, adding between 5 and 6.5 percent water by mass to produce a wet mix. This is estimated and judged by feel, as measuring the exact amount of water is difficult in practice when handling large volumes. The mixing cannot take place in a tumble mixer, as with concrete, because this causes balling of the clay and results in a non-homogenous mix. The highest quality mix is produced in a forced-action mixer, also called a vertical axis mixer. Otherwise, the traditional method of turning and spreading the material on a slab works well too, albeit with a wheel loader to save on labor. The moist mixed material should then be stored and allowed to cure, at least overnight if not a whole day, to allow the moisture to permeate throughout the mix. The wet mix should be stored with a tarpaulin cover to contain its moisture.
Photo by Lorenz Kastner
Step 6: ramming samples
After curing, produce rammed samples. Cubes of 20cm are a practical size and allow for three compacted layers. The size and geometry of the sample may also be defined by the lab conducting the compression tests. Make four samples of each mix and dry for at least two weeks. Multiple samples allow the averaging of the results. It is possible to gain a feeling for the behaviour of the material while ramming the samples: if it’s too wet or contains too much silt, the material can be very plastic and move around within the formwork while tamping; too dry or not enough clay and the gravel will bounce around and not interlock into position. The samples are also the first visual confirmation that designers and clients will have of the rammed earth’s appearance: the color, texture and horizontal striation that give rammed earth its distinctive appearance. Hone down the tops of the samples with a diamond cup wheel and abrasive pads to level the surface and reveal the composition of the mix.
Step 7: documenting results
A recipe developed by an experienced hand will perform well and be easily repeatable. But in a litigious western context, choosing a mix will ultimately be influenced most by the result of compressive tests. There are many factors that affect compressive strength, making accurate recording important. Water content, clay type, aggregate distribution, compaction equipment, mixing method and layer thickness are some of the key factors. Once rammed and removed from its formwork, weigh the test cube. It can then be left to air dry or put in an oven. When dry after two to three weeks, weigh again, and the moisture of the mix can be deter-mined by the weight lost. This method also works on loose mix before it is rammed. The compaction ratio of loose to fully compacted material can be calculated and should be roughly 50 percent reduction in height. If the compressive strength of a recipe meets the specified bench-mark, larger sample walls or mock-ups can be produced. Understanding the compaction ratio and the mixing method then informs production planning later down the line.